Plastic extrusion services for specialized industrial applications
Plastic extrusion services for specialized industrial applications
Blog Article
A Comprehensive Guide to the Refine and Advantages of Plastic Extrusion
In the large realm of manufacturing, plastic extrusion arises as a vital and very efficient process. Altering raw plastic right into constant profiles, it satisfies a myriad of industries with its remarkable convenience. This guide aims to elucidate the complex steps associated with this approach, the kinds of plastic apt for extrusion, and the game-changing advantages it brings to the industry. The taking place conversation promises to unfold the real-world impacts of this transformative process.
Comprehending the Essentials of Plastic Extrusion
While it may show up complex in the beginning look, the process of plastic extrusion is essentially straightforward - plastic extrusion. It is a high-volume manufacturing method in which raw plastic is thawed and formed into a continual profile. The procedure starts with the feeding of plastic material, in the form of powders, pellets, or granules, right into a heated barrel. The plastic is then thawed using a mix of warmth and shear, applied by a rotating screw. Once the molten plastic gets to the end of the barrel, it is compelled via a small opening known as a die, shaping it into a wanted form. The designed plastic is after that cooled, solidified, and reduced into desired sizes, finishing the procedure.
The Technical Process of Plastic Extrusion Explained
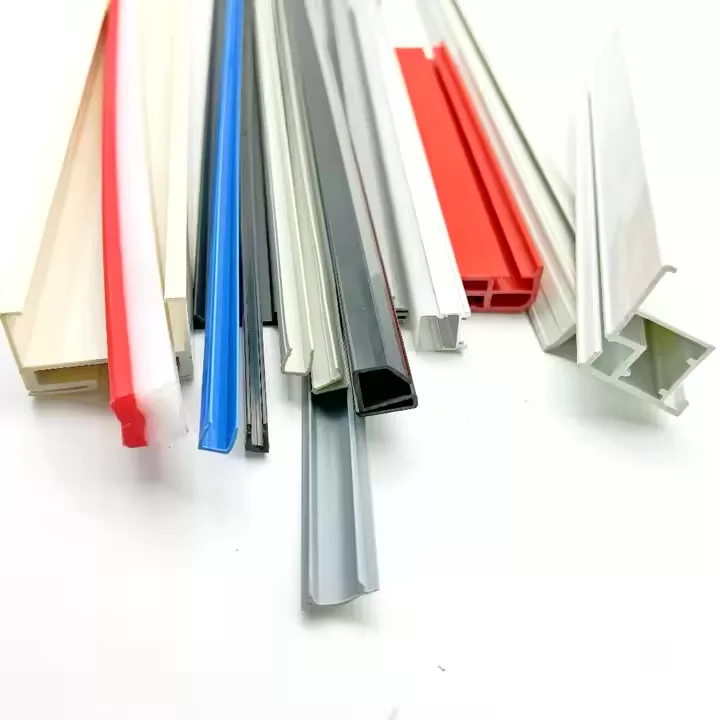
Kinds of Plastic Suitable for Extrusion
The option of the ideal kind of plastic is a crucial element of the extrusion process. Different plastics use distinct residential properties, making them much more suited to specific applications. Polyethylene, for instance, is typically used due to its low price and simple formability. It supplies exceptional resistance to chemicals and wetness, making it excellent for items like tubes and containers. In a similar way, polypropylene is another prominent choice because of its high melting factor and resistance to tiredness. For more durable applications, polystyrene and PVC (polyvinyl chloride) are usually picked for their toughness and sturdiness. Although these prevail choices, the option eventually depends on the specific requirements of the item being produced. Recognizing these plastic kinds can significantly boost the extrusion process.
Comparing Plastic Extrusion to Other Plastic Forming Techniques
Comprehending the sorts of plastic appropriate for extrusion leads the way for a more comprehensive conversation on exactly how plastic extrusion stacks up versus various other plastic developing approaches. These consist of injection molding, impact molding, and thermoforming. Each method has its unique usages and benefits. Injection molding, for circumstances, is outstanding for creating intricate parts, while impact molding is perfect for hollow items like containers. Thermoforming excels at developing shallow or large parts. Plastic extrusion is unparalleled when it comes to developing continual profiles, such as gaskets, pipes, and seals. It likewise enables a constant cross-section along the size of the product. Hence, the choice of approach mostly depends upon the end-product requirements and specifications.
Key Benefits of Plastic Extrusion in Manufacturing
In the realm of production, plastic extrusion provides lots of significant benefits. One noteworthy advantage is the cost-effectiveness of the procedure, which makes it a financially appealing production approach. In addition, this method provides exceptional item versatility and boosted manufacturing speed, consequently raising total manufacturing efficiency.
Affordable Production Technique
Plastic extrusion next page jumps to the center as an economical manufacturing method in manufacturing. In addition, plastic extrusion calls for much less energy than traditional manufacturing techniques, adding to reduced operational costs. On the whole, the economic benefits make plastic extrusion an extremely appealing alternative in the manufacturing sector.
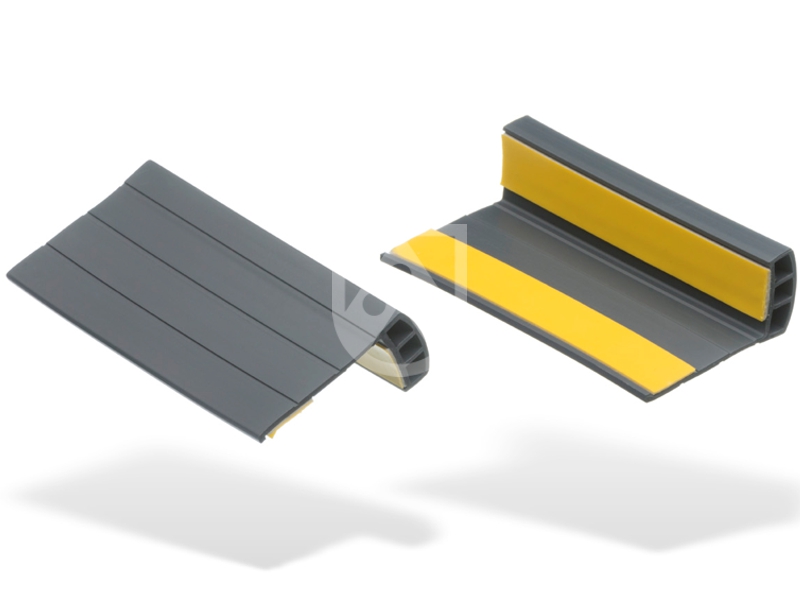
Superior Product Versatility
Beyond the cost-effectiveness of plastic extrusion, another significant benefit in producing lies in its exceptional product versatility. This makes plastic extrusion an optimal remedy for sectors that need personalized plastic parts, such as auto, construction, and product packaging. In significance, plastic extrusion's item adaptability fosters technology while enhancing functional performance.
Improved Manufacturing Rate
A substantial benefit of plastic extrusion exists in its improved production rate. Couple of other production processes can visit site match the speed of plastic extrusion. Additionally, the capability to maintain constant high-speed production without giving up product quality sets plastic extrusion apart from other approaches.
Real-world Applications and Impacts of Plastic Extrusion
In the realm of manufacturing, the strategy of plastic extrusion holds extensive relevance. The financial advantage of plastic extrusion, largely its high-volume and affordable result, has actually changed manufacturing. The industry is persistently aiming for technologies in naturally degradable and recyclable materials, showing a future where the advantages of plastic extrusion can be retained without endangering ecological sustainability.
Final thought
Finally, plastic extrusion is a efficient and extremely efficient method of changing resources into varied products. It supplies various advantages over other plastic creating approaches, consisting of cost-effectiveness, high output, very little waste, and layout flexibility. Its effect is exceptionally felt in different industries such as construction, vehicle, and durable goods, making it a crucial process in today's production landscape.
Digging deeper right into learn this here now the technical procedure of plastic extrusion, it starts with the choice of the ideal plastic product. When cooled, the plastic is cut right into the required lengths or wound onto reels if the item is a plastic film or sheet - plastic extrusion. Contrasting Plastic Extrusion to Various Other Plastic Forming Techniques
Comprehending the kinds of plastic suitable for extrusion leads the way for a more comprehensive discussion on just how plastic extrusion piles up against various other plastic creating techniques. Few other manufacturing processes can match the speed of plastic extrusion.
Report this page